
We represent several leading providers of both panelized LGS building systems as well as the manufacturing of composite foundation, floor, wall, roof and ceiling panels for residential, commercial and industrial applications. Our patented composite technology allows us to bond light-gauge cold form steel with EPS to create lightweight structural members that are capable of carrying unusually heavy loads, while providing high insulating exterior wall values (R-35 to R-65), and high resistance to fire, insects, mold and mildew. The panels are also made of partially recycled materials and are 100% recyclable. The panels have passed tests conducted by the Florida Hurricane Test Lab.
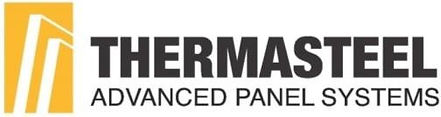
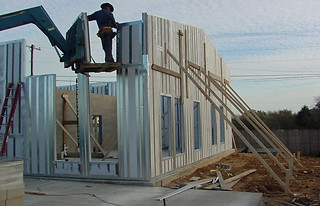
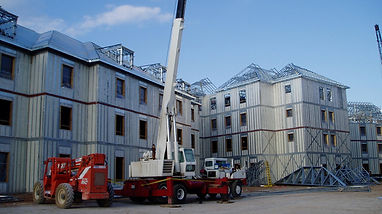
Each project comes pre-engineered and ready to assemble with door and window openings pre-cut. Panels are manufactured in a quality-controlled environment to ensure fast and trouble-free assembly on the job site. The system is used for floors, interior and exterior walls, ceilings, and roofs. Our supplier has ICC-ES, ICBO, BOCA, SBCCI and HUD approvals. It has also passed the Miami-Dade County, Florida, USA protocols at the Hurricane Test Lab.


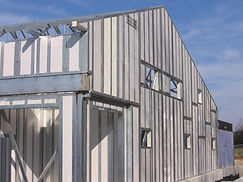
Our products have been proven in over 70,000 projects in 28 countries world-wide, including commercial as well as single and multi-family residential projects. Also, our panelized steel framing has been used in large military housing projects in the USA, Germany and Guantanamo Bay, Cuba. Production facilities are presently located in the USA from coast to coast with product being shipped via container to many other countries.
Every project is a unique opportunity to decrease build time and lower building operational and maintenance costs while providing a stronger, safer, quieter structure, that is ecologically responsible. Since project application and structural load requirements often dictate the size and type of panels needed, our standard policy is to provide quotations from architectural drawings. In most cases, we adapt plans to our system in order to maximize the benefits of our products.
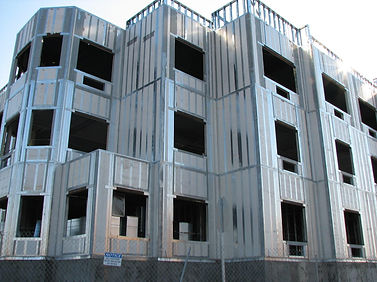
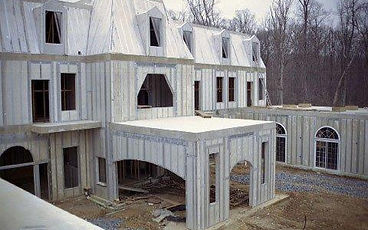
.jpg)

Cost Savings
-
The taller the structure the bigger the savings. For mid to hi rise structures, the hard framing cost savings can be between 20% to 50% versus wood and\or concrete.
-
CFS structures are more than 20% lighter than a wood structure, the saving starts from foundation.
-
CFS wall studs and floor joists are pre-punched for electrical, plumbing and HVAC ducts penetration, thus drop ceilings, soffits and all kinds of secondary framing are minimized, saving project time and cost, another 20% saving.
-
HSS hot rolled steel columns & beams are replaced by CFS built-up composite columns & beams, over 50% cost and time saving.
Time Savings
-
Versus wood framing, pre-panelized CFS framing accelerates schedules a minimum of 50% if not 75%.
-
All CFS framing panels are done parallel to site work, this leads to much faster project completion.
-
Since all pre fab work are off site, weather becomes an irrelevant factor for the project schedule.
Lower Insurance & Maintenance
-
Construction insurance cost for CFS framing is 1/5 of wood framing.
-
Building operations and maintenance cost for the structure part will be 1/10 versus wood framing.
-
CFS building will provide building owners with much higher property terminal value.
-
Reduced HVAC capacity with our insulated panel system